I'm not naturally a miser - I love spending money, I just don't have a lot of it, what with responsibilities like house, mortgage, running a car, and then there's the four kids and the daily expenditure that goes along with that (though I don't begrudge or regret a penny of it). And you don't need me to tell you there's some kind of world wide recession going on and that just like our extremely sincere and trustworthy polititians have said, we're all in it together.So, in my efforts to demonstrate austerity, I sometimes have to resort to a bit of DIY.
It was about 25 years ago that I attended a museum exhibition in Manchester about the history of slavery, and whilst I found the whole thing eye-opening and very sobering, one of the things that really struck me was a collection of hand-made knives, mostly over-sized folders and balisong type affairs, all made very crudely from lengths of steel, some from steel rules and old saw blades. And while they were very basic and crudely made, out of necessity and their makers having to work with whatever was to hand, they were functioning and fit for purpose. I had always loved knives and it suddenly struck me that it was possible to make my own; that like the knives in the exhibition, they didn't have to have professional finishes or be polished within an inch of their lives, they just needed to be sharp and strong.
This was the beginning of a much later flirt with knife making and the origin of my attitude toward most things, including brick-laying, roofing, electrics, plumming and most other aspects of DIY, whereby I will look at something and say' "I think I could do that' and then give it a go. I remember when we decided our kitchen needed extending and although I had never laid a brick before, placed a roof tile, worked with RSJs or fitted a double-glazed window, I figured it must be common sense and if I took each bit a steep at a time, it probably couldn't go far wrong, and if it did, well
then I could pay a professional to do it.
Anyway, I digress terribly. With my interest in crafts and green woodworking I often feel caught between the rock and a hard place which is the obsession with new and expensive kit and not having a lot of money to spend. I watched the video that Julian posted by Peter Galbert, whose blog I have followed for some time (though posts have been few and far between) and thought how much I would love to go on a chairmaking course and then collect together all the tools that would enable my success. But add it up, folks - specialist draw knives, inshaves, travishers, adzes, tennon cutters, etc, etc - it adds up to a fortune and for someone like me with only a casual interest (casual because time doesn't really allow for a serious foray into these crafts) it's just too much money.
So what's my point? Simple. I have been at a number of spoon carving events and seen at various times other carvers using a scorp - a sharpened ring of metal fixed to a handle for carving the bowl of a spoon.
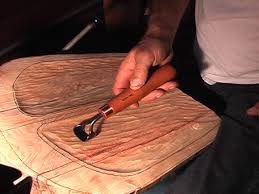 |
I couldn't find a picture of someone using one for spoon carving, but it's essentially the same thing. |
Do I need a scorp? Of course I don't. I have two perfectly good spoon knives, which is one more than I can use at any one time. But what has 'need' ever had to do with the aquisition of tools?
Having had a little go recently with Martin Damen's scorp, a tool with which he achieves some amazing results, I thought I should perhaps hace a go at making my own - or more accurately, at adapting a tool I bought from ebay some time ago. It looks (or should I say
looked) like this when I first bought it.
It was listed as a farrier's loop, they still have them on there now, for trimming horse, sheep, pig and goat hooves. It cost me £8. When it came I realized it was no good for spoons due to the long neck and angle of the head. It might be ok for bowls, but it needed regrinding to put the grind on the outside, rather than the inside - at least that's what I figured from what I'd seen of other carving tools and my own experience with an adze that had an internal grind. So I put it away in the shed and forgot about it. Until this weekend.
So, I removed the head from the handle, started to grind the existing edge flat, then figured, why not just sharpen the outside of the other side of the ring. I also hammered on the neck to straighten it out, which would have worked much better if I'd heated it first, but I didn't have the time for that.
 |
I was very pleased with the work I did on the grind - it is razor sharp. |
I showed it to Ju and he pointed out that it was probably too thick and would foul my work and chatter when used for carving, so this morning I ground off the back of the head. And here is my finished article.
I've had a quick go with a bit of scrap wood and it carves fine. I suspect I may have made the neck too short now and if this turns out to be the case when I actually try carving a spoon, then I will re-handle it in order to expose a little more. Either way, in the tradition of those knives I saw in Manchester, it is sharp, practical and fit for purpose, and for £8 and a little time grinding, I'm happier than if I'd spent £50 plus on a Two Cherries scorp. I'll try it out this weekend and let you know how I get on.